Mit 94 Mitarbeitenden gehört die Nachbur AG zu den grösseren Schweizer Zulieferunternehmen im zerspanenden Bereich. Produziert wird auf einem Maschinenpark mit rund 70 Drehmaschinen, Fräsmaschinen und Multitask-Maschinen sowie einer grossen Anzahl von weiteren Maschinen wie z. B. zum Schleifen und Laserbeschriften. Die eigene Baugruppenmontage rundet die Leistungsfähigkeit von Nachbur ab. Die Kompetenz der Nachbur liegt im Drehen, Fräsen und in der Baugruppenmontage. Geliefert wird in alle Branchen: Prozess-Regeltechnik, Medizin, Hydraulik, Luftfahrt, Optik und den allgemeinen Maschinenbau.
Komplettes Werkstoffprogramm wird bearbeitet
Dass hier nichts dem Zufall überlassen wird, versteht sich von selbst. Von Kleinserien bis zu mittelgrossen Serien fertigt das Unternehmen ein breites Spektrum an Teilen, die von der Grösse her im kleineren bis mittleren Bereich angesiedelt sind. Bearbeitet wird von Aluminium über Buntmetalle bis hin zu Duplexstählen, Nickelbasislegierungen wie Hastelloy und vieles mehr. Kurz: Es gibt fast keinen Werkstoff, der nicht bereits bei Nachbur zerspant wurde.
Auf die Frage, was im Rahmen des täglichen Fertigungsgeschehens besonders anspruchsvoll ist, sagt Roger Gränicher, Teamleiter CNC-Drehen: «Die Toleranzen passen sich kontinuierlich dem technisch Machbaren an. Es kommt immer wieder vor, dass die Toleranzfelder im µ-Bereich liegen, dann wird es anspruchsvoll. Vor allem dann, wenn es um grössere Serien mit den entsprechend hohen Anforderungen an die Prozesssicherheit geht.»
Zerspanungstechnisch anspruchsvoller Werkstoff
Im Fokus dieser Anwendung steht eine Steuerbuchse, die in der Prozess- und Regeltechnik Einsatz findet. Bei dem Werkstoff handelt es sich um einen rostfreien austenitischen Edelstahl. Da bei diesen Edelstählen der Spanbruch fördernde Schwefelgehalt sehr gering ist, sind Fliessspäne unvermeidlich. Der Zusatz von Molybdän fördert die Korrosionsbeständigkeit, welches jedoch in der Zerspanung negative Einflüsse zeigt. Je nach Bauteil, Losgrösse und Geometrie ist die Zerspanung von 1.4404 mehr oder weniger anspruchsvoll. Bei der zu fertigenden Steuerbuchse war die Problematik die ca. 70 mm lange Sacklochbohrung mit einem Durchmesser von 16 mm. Typischerweise verwendet Nachbur für solche Operationen Bohrstangen. Wegen der tiefen Bohrung und des im Verhältnis geringen Durchmessers, kam ein schwingungsgedämpftes Bohrstangensystem zum Einsatz, aber die Prozesssicherheit war aufgrund der oben beschriebenen schwierigen Spanbildung nicht perfekt.
IT9-Toleranzfeld als solches unproblematisch
Das IT9-Toleranzfeld (fünf hundertstel Millimeter) der Bohrung war als solches unproblematisch. Herausfordernd war hingegen, die Oberflächenrauheit mit der Bohrung Rz 10 prozesssicher zu fertigen. Durch die unvermeidbaren Fliessspäne, welche durch die Bohrstange nach vorne in die Sacklochbohrung geleitet werden und so zum Teil zu Beschädigungen der Oberfläche führten. Jedes gefertigte Element musste daher kontrolliert werden und es kam immer wieder zu Ausschussteilen.
Reiben als Lösungsansatz
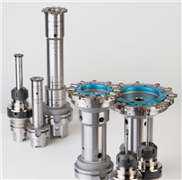

Selbst IT5-Toleranzfelder sowie sehr feine Oberflächen mit dem Reibverfahren realisierbar.
Aufgrund der hohen Stückzahlen musste der Prozess zwingend optimieren werden. Bei einem IT9-Toleranzfeld bei 16 mm Durchmesser denkt man aus rein fertigungstechnischer Sicht erst einmal nicht daran, Reibahlen einzusetzen. Doch der Präzisionswerkzeughersteller URMA AG ging diesen aussergewöhnlichen Schritt: Die Hochleistungs-Reibwerkzeuge wurden durch URMA auf die spezifische Anwendung ausgelegt und in den Prozess mit den geforderten Schnittparametern integriert. Der Einsatz von Reibwerkzeugen hat bezüglich der Flexibilität gegenüber dem Ausdrehen ein Nachteil, kann jedoch dank der bedienerunabhängigen Prozesssicherheit auf den Durchmesser, die Geschwindigkeit und die Oberflächengüte punkten.
Ist ein Werkzeug bei URMA nicht ab Lager verfügbar, werden die Hochleistungs-Reibwerkzeuge im Durchmesserbereich von 7,6 mm bis 200,6 mm je nach Kundenanforderung auf den gewünschten Durchmesser, die Geometrie sowie den optimalen Schneidstoff inkl. Beschichtung ausgelegt und hergestellt.
Von 120 Sekunden auf 12 Sekunden
Nachbur dreht seit mehr als 70 Jahren. In der Regel lassen sich alle Konturen mit üblichen Bohr- und Drehwerkzeugen realisieren. Selbst IT5-Toleranzfelder sowie sehr feine Oberflächen sind so realisierbar. Doch die Prozesssicherheit und die erforderliche Zeitreduktion hat das Unternehmen dazu bewogen auf den Reibprozess zu setzen.
Die Reiben fahren mit einer Drehzahl von 800 min-1 und einer Vorschubgeschwindigkeit von 0,14 mm pro Zahn. Bei sechs Schneiden sind das 670 mm/min. Die reine Hauptzeit der 70 mm langen Sacklochbohrung konnte, dank des neu integrierten Reibprozesses, auf 6 Sekunden verkürzt werden. Die gesamte Passbohrung wird heute inklusive Nebenzeiten neu in 12 Sekunden gefertigt. Zuvor waren es 2 Minuten.
Späne werden hervorragend evakuiert
Mit den URMA RX-Reibsystemen kann die Oberflächengüte konstant zwischen Rz 4 und 8 µm gefahren werden, mit einem Standweg bis zu 68 m. Anschliessend kann in kürzester Zeit ein neuer Wechselkopf eingesetzt werden, ohne dass das Werkstück neu eingefahren werden muss. Es geht ohne Messschnitt und allfälligen Werkstückausschuss gleich weiter mit der Produktion. Die URMA Reibsysteme zeichnen sich ausserdem durch extrem kurze Schneiden (4,3–5,3 mm) aus, womit der Span hervorragend aus der Sacklochbohrung evakuiert wird. Durch die hohe Stabilität des RX-Systems kann ein hoher Vorschub gefahren werden, was die Spanabfuhr begünstigt.
Maschinengenauigkeit hat auf die Bohrungsqualität keinen Einfluss mehr
Beim Reiben liegt die Durchmesserverantwortung auf dem Werkzeug – sie ist sozusagen maschinenunabhängig. Damit die geforderten Lagetoleranzen der Bohrung eingehalten werden, wird die Reibahle auf den ersten 3 mm durch eine angedrehte Pilotierung positioniert. Durch die Werkzeugspannung mittels Pendelfutter wird zudem der Wärmegang der Maschine ausgeglichen. Dank den RX-Reiben ist eine 100%ige Prozesssicherheit, ein schnelleres Fertigungsverfahren und eine geringere Ausschussquote sichergestellt. Matchentscheidend war jedoch, dass mit dem Reiben eine mannlose Fertigung realisiert werden konnte, da eine bedienerunabhängige Prozesssicherheit durch das Reiben erreichet wird. Nachbur analysiert die Prozesse nun kontinuierlich um Bohrungsbearbeitungen zu identifizieren, die auf Reibprozesse umgestellt werden können.
URMA AG
URMA AG entwickelt und fertigt Präzisionswerkzeugsysteme, die weltweit bei Bohrungsarbeiten in der Automobil-, Hydraulik-, Maschinenbau- sowie Flugzeugbauindustrie eingesetzt werden, um die Prozesssicherheit zu erhöhen und zur Effizienzsteigerung beizutragen. URMA hat den Hauptsitz und die Produktionsstätte in der Schweiz. Das Familienunternehmen mit 130 Mitarbeitern verfügt in Deutschland, Spanien und China über Niederlassungen und unterhält OEM-Partnerschaften mit Paul Horn (Deutschland) und Sumitomo (Japan).