Die Mechaniken von Produktions-, Montage- und Antriebsapplikationen erzeugen eine polyphone Geräuschkulisse in der neuen Fertigungshalle von Gindele. Zwei Spritzgussmaschinen geben am Eingang der komplexen Anlage den Takt vor. Es bedarf zweiundfünfzig fein aufeinander abgestimmter Prozessschritte, damit am Ende der Linie mit robusten Deckeln und Anschlüssen versehene Sekretbeutel vom Band laufen. Elf Stück pro Minute, 660 die Stunde. Im Zuge eines verzweigten Fertigungsprozesses werden Ausgangs-, Zwischen- und Endprodukte auf Fehler oder Unregelmäßigkeiten kontrolliert.
Unternehmensduo entwickelt integrierte Fertigungslösung
Die Beutel dienen dem sicheren Auffangen und Entsorgen unterschiedlicher Sekrete. „Jeder Einwegbeutel muss auf dieselbe einfache Art und Weise verschließbar sein und Flüssigkeiten überlaufsicher aufnehmen“, bringt Tobias Gindele, Leiter der Automatisierungstechnik, die zentralen Produktanforderungen auf den Punkt. „Er muss höchsten Qualitätsansprüchen genügen und darf z. B. beim Fall auf den Boden nicht platzen“. Was als fertiges Produkt kompakt und überschaubar erscheint, erweist sich in der Herstellung als durchaus anspruchsvoller Vorgang. Dieser erfordert in vielerlei Hinsicht Knowhow, integrierte Prozesskenntnisse und die Auswahl kompetenter Partner. Gindele mit Sitz in Neuhausen bei Pforzheim hat die Anlage gemeinsam mit Robomotion geplant und realisiert. Einst Hersteller hochwertiger Kunststoff-Spritzgussprodukte, entwickelt Gindele heute komplette Baugruppen und Anlagen. Als Systemintegrator übernimmt Robomotion in Leinfelden-Echterdingen die Entwicklung und Konstruktion vorwiegend robotikbasierter Applikations- und Steuerungslösungen.
Von einem namhaften Healthcare-Konzern erhielt das Unternehmensduo im Jahr 2015 den Auftrag zur Herstellung von Sekretbeuteln. Im ersten Schritt galt es, die gestellte Aufgabe in effiziente, automatisierbare und prozesssichere Fertigungsschritte zu gliedern. „Wir klären kritische Prozesse vorab über Funktionsmuster und simulieren den Ablauf am Rechner. Das schafft Vertrauen, denn unsere Kunden erkennen, dass wir uns am Ende nur mit Lösungen zufrieden geben, die definitiv die gestellten Anforderungen erfüllen“, sagt Dr. Andreas Wolf, Geschäftsführer von Robomotion.
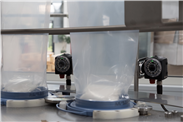

Vision Sensoren mit ihren Bildaufnehmern registrieren zuverlässig, ob der Beutel tatsächlich ein Gelpäckchen enthält (innen, auf blauem Deck
Balluff RFID-System als wesentlicher Prozessbestandteil
Im ersten Schritt entnimmt eine Greifereinheit Verschlusskappen, Stutzen und Filterdeckel direkt aus der Spritzgussmaschine. Die Teile werden auf Werkstückträgern positioniert, die mit dem Industrial RFID-System BIS M (13,56 MHz) von Balluff ausgestattet sind. Das auf IO-Link basierende System dient dem automatischen und berührungslosen Identifizieren und Lokalisieren von Objekten. Das RFID-System unterstützt weltweite ISO-Standards und bietet eine hohe Übertragungsgeschwindigkeit selbst bei großen Datenmengen. Aufgrund der vielfältigen Kombinationsmöglichkeiten von Datenträgern und Schreib-/Leseköpfen eignet sich das System sowohl zur Teileverfolgung im Nahbereich als auch für Anwendungen in der Produktionssteuerung (Palettierung, Aufzeichnung am Werkstück, Teilerückverfolgung etc.).
In der Gindele-Anlage sind sechzig Werkstückträger mit RFID-Datenchips von Balluff ausgestattet. Mit individueller Codierung versehen durchlaufen diese die ersten Montage-, Füge- und Kontrollstationen. Unmittelbar am Eingang zum Grauraum prüft ein Kamerasystem, ob sämtliche Teile lagerichtig auf dem Werkstückträger angeordnet sind. Es folgt die Montage zweier Filter und eines Verschlussdeckels, eine weitere Kamerastation kontrolliert auf korrekten Sitz. Entlang des zweibahnigen Prozesses bis zur Übernahme der Bauteile durch einen Roboter findet an zehn Schreib-/Leseköpfen ein Datenaustausch statt. Die auf dem Chip gespeicherten Produkt- und Werkstückträgerdaten gelangen zur zentralen Steuerungseinheit und werden ausgewertet. Entsprechen einzelne Werte nicht den Zielvorgaben, veranlasst die Steuerung, dass der Werkstückträger ohne weitere Bearbeitungsschritte bis an die Übergabeposition fährt. Das NIO-Bauteil wird dort ausgeschleust, der leere Träger kehrt an die Startposition zurück.
Vision Sensor prüft auf Vorhandensein von Gelpäckchen
Ein Roboter mit Greifapplikation übernimmt die gefertigten IO-Teile: Die nachfolgende Station setzt ein Rückschlagventil auf den Stutzen an der Deckelunterseite, eine Prüfkamera kontrolliert, ob dieses den Vorgaben entsprechend angebracht ist. Auf dem anschließenden Rundtakttisch wird der Folienschlauch zugeführt, der später zum Sammelbeutel wird. Eine Reflexionslichtschranke von Balluff prüft, ob der Schlauch tatsächlich vorhanden ist. Passgenau zugeschnitten weitet ein Spreizer die Folie, stülpt diese auf die Deckelunterseite und verschweißt beide dauerhaft miteinander. Ein Zylinderschalter von Balluff übernimmt die Endlageabfrage im Pneumatikzylinder: Diese Magnetfeld-Sensoren dienen vorwiegend der Überwachung von Kolbenposition an Zylindern und Greifern. Der Sensor erkennt dabei das Feld des im Kolben integrierten Magneten durch die Aktorwand hindurch. Im Unterschied zu herkömmlichen Reed- bzw. mechanischen Schaltern bieten die elektronischen, magnetfeldempfindlichen Sensoren ein zuverlässiges und prellfreies Schaltverhalten bei erheblichen Funktionsreserven ohne Fehl- und Doppelschaltpunkte.
Um dem Anwender ein Höchstmaß an Sicherheit zu bieten und einfließendes Sekret zu binden, lässt das Healthcare-Unternehmen einen Teil der Beutel mit Gelpäckchen ausstatten. Die Päckchen werden über ein Wickelband zugeführt, eine Gabellichtschranke detektiert die gewünschte Schnittposition zwischen den Gelkissen, die nach dem Schneiden in den nach oben offenen Schlauch fallen. Gabellichtschranken BGL von Balluff mit Sender/Empfänger in einem Gehäuse detektieren hochpräzise und sind bereits ab Werk justiert. Das reduziert den Aufwand, spart wertvolle Zeit bei der Inbetriebnahme und unterstützt einen zuverlässigen Prozess. Die nachfolgende Kameraprüfung stellt sicher, dass in jedem Schlauch ein Gelpäckchen liegt. „Hier hatten wir zunächst auf konventionelle Sensorlösungen gesetzt, das hat aber nicht in jedem Fall funktioniert. Mit den Vision Sensoren von Balluff haben wir an dieser Stelle hundertprozentige Sicherheit“, betont Tobias Gindele. Mit seinem CMOS-Bildaufnehmer erkennt der Vision Sensor vorgegebene Merkmale lageunabhängig im gesamten Erfassungsbereich. Unabhängig voneinander verarbeitet er bis zu sieben Inspektionsaufgaben, darunter Kanten zählen, Helligkeit und Konturen prüfen, Kontraste vergleichen, Muster erkennen und Positionen finden. Über die SPS lassen sich ganz einfach bis zu 20 speicherbare Inspektionen aktivieren.
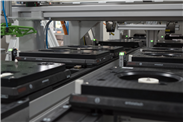

: Industrial RFID-System BIS M von Balluff: Werkstückträger identifizieren sich an den Schreib-/Leseköpfen und tauschen Daten aus
Mit den Signalleuchten SmartLight von Balluff alles im Blick
Es folgt das Verschweißen und anschließende Schneiden der Schlauchfolie, zwischen zwei Klemmbacken wird auf Dichtheit geprüft. Eine Roboter entnimmt die Teile aus dem Rundtisch und schließt die Deckel. Quasi en passant erhält jeder Beutel einen Aufdruck und damit seine individuelle Kennung. An zahlreichen Stationen sind, für den Anlagenbediener gut sichtbar, IO-Link Signalleuchten SmartLight von Balluff angebracht. Mit ihnen lässt sich eine große Bandbreite an Zustandsanzeigen, Warnbotschaften oder Handlungsaufforderungen auf einfache Weise visualisieren. Farben und Zonen sind nicht fest zugewiesen, sondern frei programmierbar. Mit SmartLight lassen sich wahlweise Segment-, Level-, Lauflicht- und Fleximodi mit einem breiten Farbspektrum darstellen.
Eine letzte Kamera prüft auf Fehler und Vollständigkeit, mit dem seitlichen Falten und dem Ablegen des Beutels im Karton endet der Herstellungsprozess. Um auf Nummer sicher zu gehen, legt der Roboter jeden sechsten Beutel auf einen separaten Übergabetisch: Der Anlagenbediener kontrolliert den Sekretbeutel zusätzlich optisch auf erkennbare Fehler und Auffälligkeiten.
Beratung, Service und der persönliche Kontakt entscheiden
Die Fertigungsanlage von Gindele/Robomotion zeigt eindrucksvoll, dass intelligente, flexible und effiziente Robotiklösungen längst auch bei kleineren Mittelständlern angekommen sind. Ausschlaggebend für den Erfolg und die Zuverlässigkeit ist nicht zuletzt die Wahl der richtigen Projektpartner: „Wir legen größten Wert auf verlässliche, langfristige Partnerschaften. Laufende Wechsel können wir uns nicht leisten. Dazu muss neben der Produktqualität die Beratung, der Service und der menschliche Kontakt stimmen. Bei Balluff sehen wir uns diesbezüglich seit Jahren sehr gut aufgehoben“, fasst Dr. Andreas Wolf zusammen.