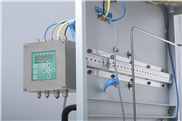

Purge Controller 6500 mit automatischer Überwachung und Kontrolle von Gehäusedruck und -temperatur.
Einsatz von Wasserstoffanalysegeräten im Ex-Bereich ermöglichen Das Konzept der Überdruckkapselung besteht darin, die verbauten elektrischen Betriebsmittel von der explosionsfähigen Atmosphäre zu separieren. Dazu verwendet man ein Gehäuse, welches mit einem für die jeweilige Ex-Zone oder Division zugelassenen Überdruckkapselungssystem bestückt wird. Um die Überdruckkapselung zu ermöglichen, wird das Gehäuse zunächst durch Druckbeaufschlagung ‚gereinigt‘. Dies erfolgt entweder mit einem Inertgas oder sauberer Luft. Nach der Reinigung wird mit Hilfe der Regelung im Inneren des Gehäuses ein minimaler Überdruck (wenige Millibar) aufrechterhalten. Zum Überdruckkapselungssystem zugehörige Komponenten wie Ventil und Druckwächter überwachen und stellen sicher, dass keine Ex-Atmosphäre in das Gehäuse eindringen kann. So können auch konventionelle Elektrogeräte wie Analysatoren im Ex-Bereich eingesetzt werden. Im Fehlerfall reagiert die Steuereinheit. Diese meldet nicht nur, sie schaltet im Notfall die Anlagen auch sicher ab. Dies geschieht jedoch nur, sofern ein voreingestellter Minimaldruck unterschritten wird. Bei leichten Druckabfällen gleicht die Leckage-Kompensation den Druckverlust aus. Dies ermöglicht, den Fehler im laufenden Betrieb zu beheben.
Eine solche Gehäuselösung zur Analyse der Wasserstoffqualität wünschte auch ein grosser, in den USA ansässiger Hersteller für Analysegeräte. Ziel war es, ein Produkt zu entwickeln, welches Anbietern von Wasserstofftankstellen ermöglicht, die Qualität des Wasserstoffs direkt an den Zapfsäulen sicherzustellen. Dabei sollen drei dafür entwickelte Analysegeräte prüfen, ob alle Normvorgaben zur Wasserstoffqualität eingehalten werden. Denn je nach Herstellungsverfahren können im Wasserstoff unterschiedlichste Verunreinigungen auftreten. In diesem Fall werden sieben verschiedene Gase detektiert und analysiert. Der Kunde ist dabei an Pepperl+Fuchs herangetreten, für ihn eine Ex-fähige Gehäuselösung zu entwickeln. Der Kunde hatte eine Vielzahl an bestimmt Anforderungen und wünsche welche in das Design integriert werden mussten. Der Kunde stellte das eigenentwickelte Equipment zur Verfügung und vertraute Pepperl+Fuchs, einem Experten auf diesem Gebiet, eine praktikable und sichere Lösung zu entwickeln.
Vollständig zertifizierte und einsatzfähige Plug&Go Lösung Pepperl+Fuchs übernahm das Engineering, inklusive der Auswahl eines passenden Schranks, und entwickelte eine Lösung. Das Ergebnis war eine direkt einsatzfähige Gehäuselösung mit Analysegeräten, verwendbar in den Zonen 1, 21 und 2, 22. Die Ingenieure achteten zudem auf die kleinen, jedoch wichtigen Details. Um beispielsweise eine einfache Wartung zu gewährleisten, wurden vorne und hinten am Schrank Türen eingebaut. Das bietet die Möglichkeit, die Analysegeräte zu inspizieren, ohne diese vorher ausbauen zu müssen. Zudem wurden Rohre aus speziellem Edelstahl zu den Analysegeräten gelegt, die für den Einsatz mit Wasserstoff notwendig sind. Die Projektingenieure von Pepperl+Fuchs übernahmen ausserdem die vollständige Zertifizierung und den Bau der Gehäuselösung nach ATEX- und IECEx-Richtlinien. Das Schutzniveau Ex pxb der Überdruckkapselung entspricht dabei der Zulassung gemäss Norm IEC 60079-2 für die Zone 1.
Diese vollständig zertifizierte und direkt einsatzbereite Lösung wird nun Betreibern von Wasserstoffbetankungsanlagen als Standardlösung angeboten. Es handelt sich somit nicht um ein einmaliges Projekt, sondern um eine für Kunden höchst flexible Lösung. Endkunden kaufen ein Produkt, welches vor Ort direkt einsatzbereit ist. Schnelle Analysen bei zuverlässigem Explosionsschutz sind bei höchster Betriebssicherheit garantiert.
Langjähriger Partner in der Prozessindustrie Auch viele andere Partner profitieren vom umfangreichen Know-how von Pepperl+Fuchs. Engineering-Teams, verteilt auf weltweit sechs Solutions-Engineering-Centers (SEC), finden für den Kunden stets die wirtschaftlich und technologisch beste Lösung. Die Produktspezialisten übernehmen dabei Engineering, Design, Zertifizierung und Bau der massgeschneiderten Steuerungs- und Verteilungslösungen. Nach gemeinsamer Abnahmesind die Lösungen sofort einsatzbereit und können an ihren vorgesehenen Einsatzort geliefert werden.